Apollon-Q PP Operating Instructions
Are you looking for the Apollon-Q PP operating instructions?
Here you will find the operating instructions for the Apollon-Q PP
Symbols and explanations
📢 Warnings and important information about possible hazards or damage
💡 Important information required for a smooth operation of the devices
Safety instructions
📢 Please note:
- Observe the safety instructions and installation instructions in the manual and in the installation list.
- Ensure that the installation environment complies with the prescribed guidelines for the area of application. Observe the temperature and other limit values at all times.
- The device may only be used in the areas specified in the technical data.
- The device may only be used for the intended purpose described.
- Safety and function are no longer guaranteed if the device is modified or extended.
📢 If the device is not installed correctly:
- It may not function properly.
- It may be permanently damaged.
- It could pose a risk of injury.
📢 Please note:
- Improper handling such as improper mechanical stress, e.g. by dropping the appliance, can lead to damage.
Technical drawing
💡 Please refer to the further description:The front is the side on which the logo and the central opening for the sensor are located. The back is the side on which the lettering (company address etc.) can be seen.
General function of the Apollon-Q PP
The Apollon-Q PP is a sensor for detecting the presence of objects and goods. The sensor can be used, for example, to detect parcels or pallets on shelves.
In the example, a shelf with four stacked items is used.
Depending on the set measuring frequency, the sensor detects the presence of the packets via an optical time-of-flight distance measurement. The measuring frequency can be set via the “Measuring period” (mper) parameter. The default value is 5000ms.
For reliable detection of the packages, the distances should always be set to approximately half the height of the packages, as shown in the figure. l4d should therefore be the distance from the sensor to package 4 plus half the height of package 4. If the measured distance of the sensor is less than the set distance l4d, the sensor has detected an object in the area of level 4.
If package 4 is on the shelf, the sensor returns the following values in the payload:
...
object_present: true,
object_level: 4,
object_distance: [Distance to the object],
...
If package 4 is removed from the shelf, a beep sounds and the sensor sends a message due to the change in status. The distance is now measured and compared with the set levels. In this case, the measured distance is less than the set distance l3d and the sensor has detected an object at level 3. Here the sensor returns the following data in the payload:
...
object_present: true,
object_level: 3,
object_distance: [Distance to the object],
...
This behavior can be applied analogously to the removal of packages 1 to 3.
If a distance outside the defined limit values is measured, the sensor transmits a change of state from level 1 to no object detected and adjusts the payload as follows:
...
object_present: false,
object_level: 0,
object_distance: [Distance to the objectt],
...
This status is set if a distance greater than l1d is detected. If there is no parcel on the shelf, this is acknowledged with object_present: false.
The sensor transmits the data no later than the defined measuring period for each status change. A handshake can also be configured.
Up to 4 different levels can be defined in the sensor. The values can be configured via NFC or downlinks:
Name | Description | .json key |
Distance level 1 | Distance to trigger level 1 change of state | l1d |
Distance level 2 | Distance to trigger level 2 change of state | l2d |
Distance level 3 | Distance to trigger level 3 state change | l3d |
Distance level 4 | Distance to trigger level 4 change of state | l4d |
l1d always represents the greatest distance, i.e. the distance to the object that is furthest away from the sensor.
l1d always represents the smallest distance, i.e. the distance to the object that is closest to the sensor.
Not all distances always have to be defined. If you only want to differentiate between two objects, you can use the lvls parameter to set the number of active stages/levels. The levels are then activated in ascending order. If the parameter lvls = 2, the distance level 1 (l1d) and the distance level 2 (l2d) can be set.
The dyn parameter can be used to set whether the sensor can distinguish between current levels or not. If dyn=1, the sensor returns the current level, distance and object_present, if dyn=0, the sensor only returns object_present:true or object_present:false.
Looking at the present case, the number of levels lvls=2 can be set to fulfill the use case. In this case, the maximum fill level of the shelf is two packages.
Further applications
Depending on the configuration of the sensor, different use cases can be mapped. The following scenarios have been implemented as examples:
1. detection and presence of vehicles (industrial trucks, cars, trucks, etc.)
2. detection of open doors or flaps
3. detection of parcels in shipping boxes
Recommended fastening methods
Type | Recommended accessories | Item number Sentinum | Manufacturer |
Screws (wall)
|
DIN912 cylinder head screws or wood screws with dowels depending on the material Permissible sizes: - DIN screws M4 or M5 - Wood screws 4mm to 5 mm - - |
- | - |
Magnet |
Nedoym magnet M4 internal thread
|
- | - |
Glue
|
Assembly adhesive
|
- | - |
Adhesive stickers
|
Double-sided adhesive tape
|
Mounting accessories
Art. Item number
|
Recommended accessories
|
---|---|
Z-APOQ-MAG-NEO
|
APOQ ferrite magnet set
|
Z-APOQ-MAG-FER
|
Magnet set APOQ Ferrite
|
Z-APOQ-RWM-BN
|
Rear panel mounting set with blind rivets
|
Z-APOQ-RWM-NM
|
Rear panel mounting set with M4 rivet nuts
|
Z-APOQ-VWM-BN
|
Front panel mounting set with blind rivets
|
Z-APOQ-VWM-NM
|
Front panel mounting set with M4 rivet nuts
|
Z-APOQ-AP
|
Spacer plate PA
|
Z-APOQ-KLEBER
|
Assembly adhesives
|
Z-APOQ-SCHRAUBEN
|
Machine screws DIN912 with M4 nuts
|
Z-APOQ-SPX
|
Wood screws |
Z-APOQ-DKLB
|
Double-sided adhesive tape |
Installation and preparation
💡 If the sensor is easily accessible after installation, install the sensor first and activate it after installation!
If the sensor is no longer accessible after installation, activate the sensor first and install it after activation!
📢 Before this type of installation, make sure that the surface on which the sensor is to be screwed is flat, otherwise the housing may be damaged.
📢 The tightening torque of the screws is.
- If you have ordered a device with an external antenna, which can be recognized by the gold RP-SMA connector, first install the antenna included in the scope of delivery.
- The sensor should be mounted with the long side on a container. This means that the long side of the sensor and the long side of the container should run parallel.
- Ensure that the sensor has as free a field of view as possible. The opening angle can be described with a cone of 40°.
- Spacer plate: The spacer plate can also be used for front or rear mounting. The spacer plate ensures that a flat installation is possible and guarantees the minimum distance between the sensor and the container. In this way, the antenna performance is not impaired. If necessary, the spacer plate can also be used for rear wall mounting.
💡 External antenna: Please note that the antenna should always be mounted vertically and that the tip should point to the sky if the application allows it. The antenna should be at least 2 cm away from metal surfaces. Ensure that the antenna is not shielded by surrounding metal parts, if the application allows this. Internal antenna: If your device has an internal antenna (no external antenna visible), the Helios sensor should always be mounted with the long side vertical, as this allows the maximum signal strength of the device to be achieved. The antenna is located on the top (logo side) of the housing and should be at least 2 cm away from metal surfaces. Ensure that the antenna is not shielded by surrounding metal parts, as far as the application allows.
📢 Please note: If you receive a device with an external antenna, never operate the device without an external antenna! This can lead to irreparable damage to the sensor.
General installation instructions
The sensor measures the distance to the object optimally when it is aligned parallel to it. In the case of lumpy or pourable material, the sensor should be mounted parallel to the base of the container. Ideally, the sensor beam hits the object to be measured at an angle of 90°.
If the sensor is not mounted parallel to the object to be measured, the measuring performance may be impaired. If the sensor is not aligned horizontally, ensure that the percentage calculation of the fill level is adjusted.
Rear wall mounting with screws
This type of fastening is usually used to fasten the sensor in a container. Insert the appropriate screws into the holes provided. Alternatively, suitable wood or plastic screws can also be used if the sensor is to be attached to the respective materials. Use the two-point bracket supplied for this purpose.
If the sensor is not mounted parallel to the measurement object, the measurement performance may be impaired. In the case of non-horizontal alignment, ensure that the percentage calculation of the level is adjusted.
Front wall mounting with screws
This type of mounting works in the same way as the “rear wall mounting with screws”.
📢 Always use the spacer plate for this type of installation to ensure the distance between the antenna and the wall.
Rear panel mounting with magnets
The magnets shown below are neodymium magnets. Other versions may vary.
Insert the appropriate magnets into the holes provided. The magnets shown here are NEODYM magnets. Alternatively, you can carry out this step for FERRIT magnets in the same way.
Insert the screws included in the set into the holes on the opposite side and tighten the magnets.
📢 Although NEODYM magnets offer a higher force per surface area, they are only suitable for outdoor use to a limited extent. Please contact us for advice if required.
💡 Optional: Pull the anti-slip covers over the magnets.
The anti-slip cover prevents the magnet from slipping when the object vibrates or changes position.
Front wall mounting with magnets
Please follow the instructions under “Rear wall mounting with magnets” to mount the magnets and screws in the opposite direction. The magnets are inserted into the holes on the front of the housing (logo side), the screws are inserted from behind.
Scope of delivery for mounting with blind rivets or blind rivet nuts
Rivet nuts
💡 What is a blind rivet nut: A blind rivet nut is a type of fastener that is used to insert threads into thin materials such as sheet metal, plastic or wood. It consists of a sleeve with a thread on the inside and a rivet on the outside. The rivet is inserted into the material with a special tool and presses the sleeve together, embedding the thread in the material. The blind rivet nut is often used when it is not possible to fit a nut on the back of the material, as the rivet nut is inserted from one side of the material and the thread on the other side is available for screwing in a screw or bolt. A special tool is required for installation, known as a blind riveting tool.
Spacer sleeve for blind rivets for insertion into the back of the housing for front panel mounting
Spacer sleeve for blind rivets for insertion into the back of the housing for front panel mounting
4x40 Blind rivets
Blind rivet nut (variant with countersunk head)
DIN912 cylinder head screw M4x40 for front wall mounting with blind rivet nuts, DIN912 cylinder head screw M4x30 for rear wall mounting with blind rivet nuts)
Drilling template
General information on pre-wall installation with blind rivet nuts
Step 1: Prepare materials and tools
Make sure you have all the necessary materials and tools to hand. You will need a blind rivet nut, riveting pliers, a drill, a drill bit, a measuring device and a wrench or pliers.
Step 2: Drill the hole
Drill a hole in the material into which the blind rivet nut is to be inserted. The diameter of the hole should be 0.1 mm larger than the outer diameter of the blind rivet nut.
Step 3: Inserting the blind rivet nut
Insert the blind rivet nut into the hole by pushing it through the hole.
Step 4: Fastening the blind rivet nut
Place the riveting pliers on the blind rivet nut and tighten the pliers to secure the blind rivet nut.
Step 5: Using the riveting pliers
Use the riveting pliers to insert the blind rivet nut into the material. Tighten the pliers until the blind rivet nut is fully embedded and forms a firm connection.
Step 6: Inspection
Inspect the blind rivet nut to ensure that it has been properly installed and forms a tight connection. If necessary, tighten it with a wrench or pliers to make sure it is securely fastened.
Vorderwandmontage mit Blindnietmuttern
📢 Always use the spacer plate for this type of installation to ensure the distance between the antenna and the wall.
Front wall mounting is used if you want to attach the front of the Apollon Q sensor to the wall of the object to which the sensor is to be attached. The front side is the side with the opening in the middle, on which the logo is also visible. This mounting method is the preferred option as it allows for easy battery or SIM card replacement by simply loosening the screws (as opposed to front wall mounting with blind rivets).
📢 Activate the sensor before starting the installation.
Step 1: Depending on the sensor type (Radar and ToF only), drill the appropriate holes in the wall to which you want to attach the sensor. Use the drilling template for this. The holes for the blind rivet nuts should have a diameter of 6.1 mm.
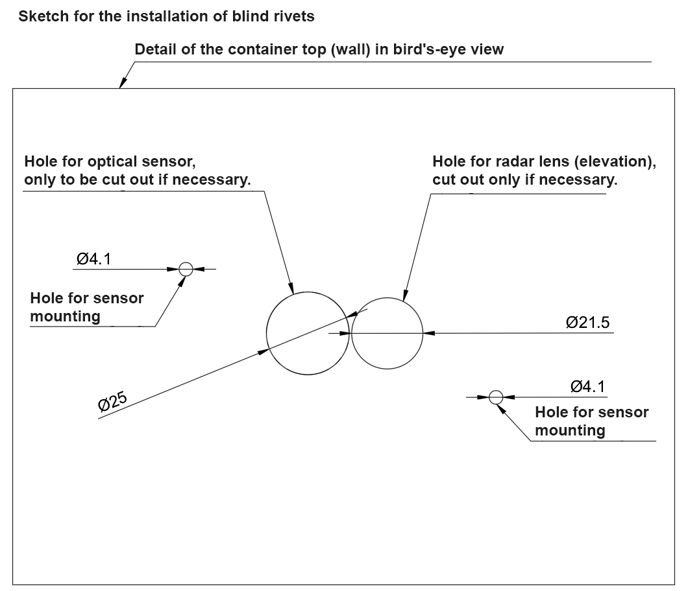
-1.png?width=688&height=532&name=Untitled%20(57)-1.png)
View of the container wall from below with the sensor mounted from above (front wall mounting). Left hole for the optical sensor, right hole for the radar sensor.
Step 3: Now the sensor is mounted.
Rear panel mounting with blind rivet nuts
Rear panel mounting works in the same way as front panel mounting with blind rivet nuts. In this case, the back of the sensor rests against the wall.
M4x30 screws are used for this type of mounting. Mounting is carried out without a spacer plate.
General information on blind rivet installation
Step 1: Prepare materials and tools Make sure you have all the necessary materials and tools to hand. You will need a blind rivet, a rivet gun and, if necessary, a drill and a drill bit.
Step 2: Drill a hole (optional) If no hole is available, drill a hole in the material in which the blind rivet is to be installed. The diameter of the hole should be 0.1 mm larger than the diameter of the blind rivet.
Step 3: Inserting the blind rivet Insert the blind rivet into the rivet gun and push it through the hole in the material.
Step 4: Using the rivet gun Place the rivet gun on the head of the blind rivet and tighten the gun to tension the rivet.
Step 5: Setting the rivet Use the rivet gun to set the blind rivet. Tighten the gun until the rivet is fully embedded and forms a secure connection.
Step 6: Check Check the blind rivet to ensure it has been set correctly and forms a secure connection. If necessary, tighten it further with a wrench or pliers to make sure it is securely fastened.
Rear panel installation with blind rivets
Rear panel mounting works in the same way as front panel mounting with blind rivet nuts. In this case, the back of the sensor rests against the wall.
4x40 blind rivets are used for this type of mounting. Mounting is carried out without a spacer plate.
The clamping range is 3 mm to 6 mm.
The holes for the blind rivets have a diameter of 4.1 mm.
Step 1: Depending on the sensor type (radar and ToF only), drill the appropriate holes in the wall on which you want to mount the sensor. Use the drilling template for this. The holes for the blind rivets should have a diameter of 4.1 mm.
Step 2: Insert the rivets through the tabs provided. Use the spacers supplied (the longer version). Insert the blind rivets first through the spacers and then through the tabs on the sensor. Now rivet the blind rivets with a suitable tool.
Step 3: The sensor is now mounted..
Front wall mounting with blind rivets
📢 Always use the spacer plate for this type of mounting to ensure the distance between the antenna and the wall.
Front wall mounting is used if you want to mount the front of the Apollon Q sensor on the wall of the object in which the sensor is to be installed. The front or front side is the side with the opening in the middle, on which the logo is also visible.
📢 Activate the sensor before starting the installation. Otherwise,
4x40 blind rivets are used for this type of installation. Mounting is done with a spacer plate.
The clamping range is 3 mm to 6 mm.
The holes for the blind rivets have a diameter of 4.1 mm.
Step 1: Depending on the sensor type (radar and ToF only), drill the appropriate holes in the wall in which you want to install the sensor. Use the drilling template for this. The holes for the blind rivets should have a diameter of 4.1 mm.Step 2: Insert the rivets through the tabs provided. Use the spacers provided (the shorter ones). Insert the blind rivets first through the spacers, then through the tabs on the sensor and finally through the spacer plate. Now rivet the blind rivets using a suitable tool.
Step 3: Now the sensor is mounted.
Hall-Switch magnetic switch Installation instructions
💡 There are two Hall sensors (magnetic field switches) on the sensor. The following diagram shows the position of the Hall sensors and the recommended placement of the magnets.
- Both magnetic field switches are active. Either one or both sensors can be used.
- Large neodymium magnets are recommended. These should be placed as close as possible to the sensor. A recommended distance between the magnet and the sensor cannot be specified universally due to the variable size of the magnet. A maximum distance of 1 cm between the magnet and the housing is recommended.
- For comparison: With a neodymium disk magnet with d = 20mm and h = 5mm, reliable values are achieved at distances of less than 1 cm.
- The magnetic field switches can be operated in three different modes:
- Container is closed when the magnet is applied.
- The container is open when the magnet is applied.
- The sensor counts an opening when the magnet passes through twice.
NFC commissioning and locating the NFC tag Activation takes place via an NFC app.
- Activation takes place via an NFC app. A smartphone is required for this. The app can be downloaded from the respective app stores. Simply search for “Sentinum LinQs” and download the LinQs app.
- First place the tag on the sensor and then place the reader on your device. The position of the NFC tag can be found in the following illustrations.
- Open the app and activate the sensor. To start the sensor in the basic settings, click on the “Activate sensor” button in the app's start menu. Now place your device on the NFC mark on the sensor.
- When the sensor is activated, “Sensor updated!” is displayed. You can then continue with the activation of the other sensors.
Replacing battery
- Open the case with a special Torx screwdriver. Carefully remove the cover and make sure the seal is not damaged.
- Carefully remove the cells from the designated holder and insert the new cells. In order to achieve the run times and power levels indicated in the datasheets, the following primary cells are allowed:
a. For LoRaWAN® and mioty® sensors
- Energizer® Ultimate Lithium Batteries - AA
- VARTA ULTRA LITHIUM Mignon AA
b. For cellular sensors (NB-IoT and LTE-CAT-M1)
- VARTA-CR-AH-R
Each sensor requires 2 cells. - When the replacement is complete, dispose of the old cells properly. Then unscrew the housing. Make sure the original position of the seal has not been changed.
📢 If cells other than recommended are used, performance and product safety may be impaired.
Labelling and certification